Printing Inks
Use of Dewaxed Bleached Shellac in Printing Inks
Use of Dewaxed Bleached Shellac in
Printing Inks
Shellac as a binder in printing ink imparts excellent toughness, adhesion and hardness so that such inks are suitable for printing on glassine paper, cellophane, metal foil and other hard and flexible surfaces.
Aniline inks:
Shellac with its hardness and elasticity is the most suitable of all resins as a binder in aniline inks. The following is a typical composition.
Dewaxed bleached shellac | 4 lbs |
Alcohol | 800 ml |
Dye | d.5 lb |
The dye is first dissolved in the alcohol followed by the addition of the shellac to the cold solution. The ink may be pigmented. Titanium dioxide has the best hiding powder and tinctorial strength as a white pigment.
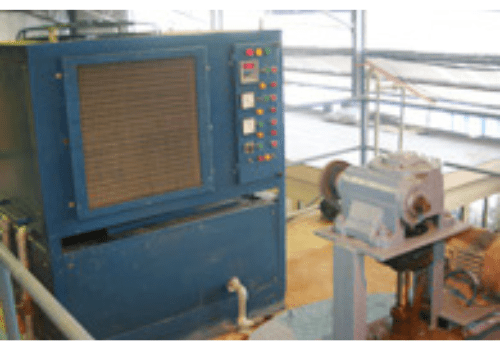
Shellac in these inks can be saponified by means of alkali in the presence of water and a high boiling solvent e.g.., Glycol, a polyglycol or there monethers.
The (printing) ink may also consists of ethyl cellulose with a dye and alcohol, titanium dioxide, shellac and methyl-cyclohexanone.
Photogravure ink (alcoholic)
A waterproof gravure ink has the following composition.
Hansa yellow | 200 gm |
Shellac solution in ethyl alcohol (1:1) | 500 gm |
Borax | 50 gm |
Ethyl Alcohol | 250 gm |
The ingredients are mixed together in a pebble mill.
In place of borax, other bases, inorganic or organic, may also be used.
Light fast printing inks:
A diluent or varnish for light fast colours for printing purposes has the following composition.
Fish (train) Oil | 2.5 Kg |
Shellac | 9 Kg |
Turpentine | 1 Kg |
Toluol/Turpentine Oil | 30/10 Kg |
The first three ingredients are stirred and heated together to uniformity and the mass, while still warm, dissolved in the solvent.
Colour for the same may be prepared of the following composition.
A | |
Basic aluminium acetate | 100 g |
Alizarin (turkey red) oil | 600 g |
B | |
Biebrich scarlet | 10 g |
Alizarin (turkey red) oil | 100 g |
C | |
Naphthalene | 30 g |
Fish (train) oil | 70 g |
These three are separately compounded and mixed together.
Magnetic printing inks:
An ink of good magnetic and printing properties and good resistance to light and chemicals is prepared of the following composition.
Shellac | 38 parts |
Diethylene glycol | 38 parts |
Triethanolamine | 4 parts |
Ethyl alcohol | 35 parts |
Barium ferrite | 16 parts |
The first four ingredients are mixed together in a ball mill. The barium ferrite is then mixed and the viscocity of the mixture adjusted to 4000 cp. With more ethyl alcohol.
Silk Screen Printing:
Shellac is used as a base for one of the colours for multicoloured silk screen-printing.
Stencil Spray Printing Inks:
A dilute solution of shellac combined with pigment and/or soluble dyes is used as spencil spray printing inks. It dries rapidly.
Lithographic Solution:
A non actinic solution which is resistant to the usual ink solvents, for use in the preparation of lithographic printing plates has the following composition.
Shellac solution (1 part of lac dissolved in 2 parts of alcohol) | 4 oz |
Alcohol | 4 oz |
Amyl acetate | 4 oz |
Oil of cinnamom | 4 dr |
Oil of lavender | 4 dr |
Methyl violet aniline crystals | 25 gm |
Fluorescent lithographing ink.
A | |
Dewaxed bleached shellac | 4.5 parts |
Methyl alcohol | 3.5 parts |
Auramine o | 7/6 parts |
Butyl lactate | 1.5 parts |
Rhodamine b extra | 1/32 parts |
B | |
Aluminium hydroxide | 3 parts |
Saponified linseed oil | 7 parts |
The ingredients of A are first stirred together till the shellac and the dyes are dissolved. Ingredients of B are then added and the mixture milled together in a roller mill till the methyl alcohol volatilises off.
The volatilisation of the alcohol can be hastened and risk due to concentration of alcohol vapour reduced by mixing with the above mixture 3.5 parts of water before the milling operation.
Printing ink for cellophane:
Dewaxed bleached lac | 44 parts |
Dye | 10 parts |
Methylated spirit | 44 parts |
Glacial acetic acid | 2 parts |
This ink, which is transparent, can be made opaque by grinding in suitable pigments.
Printing ink for cellulose ester films:
Diacetone alcohol | 200 gm |
National nigrosine base n | 20 gm |
Dewaxed bleached shellac | 80 gm |
The nigrozine is dissolved in the alcohol, filtered and the shellac then dissolved in the clear filterate. Spirit soluble dyes other than nigrozine may be used for obtaining different colours. The rate of drying can be increased by addition of methyl acetone or retarded by using triacetin. Other solvents which may be used are ethyl lactate and diethylene glycol.
The rapid drying ink, when applied, is resistant to abrasion, photographic developing and washing fluids, and non reactive to sensitised photographic emul
Water proof stamping ink for metals:
Dewaxed bleached shellac | 6lbs |
Aniline dye | 3ozs |
Denatured alcohol | 4 gallons |
The quick drying non-setting waterproof ink is suitable for stamping on metal sheets.
Marking ink for aluminius:
Dewaxed bleached shellac | 15 gm |
Methylated spirit | 35 gm |
Maleic anhydride | 0.15 gm |
Pine oil | 0.75 gm |
Rhodamine b | 0.075 gm |
Printing ink for aluminium foil:
Dewaxed bleached shellac | 60 lbs |
Denatured alcohol (95) 0%) | 180 lbs |
Butanol | 80 lbs |
Butly acetae | 80 lbs |
Dibutyl phthalate | 3 lbs |
Phosphoric acid (10% of 85% In methanol) | 24 lbs |
The shellac is dissolved in the alcohol, and the butanol, butyl acetate and the dibutyl phthalate then stirred into this solution. The phosphoric acid solution is then added and well stirred and the mixture allowed to stand for about five hours. The composition is finally filtered free from the slight precipitate (of wax) if any.
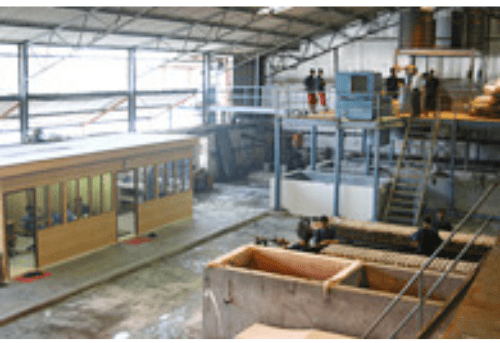
Printing ink for waxed pellets:
A vehicle composed of dewaxed bleached shellac (confectioner’s glaze), ethyl alcohol, butyl alcohol, cyclohexane and ammonia is pigmented with urified carbon black and a food dye or pigment e.g. D & c blue no.6 (colour index vat.blue 1). This ink is suitable for application to waxed pellets in any conventional pellet printing machine.
Printing lacquer for textiles:
A highly flexible composition of good covering power suitable for roll printing on fabrics, that will not “crock” or “dry mark off” is prepared of the following composition.
Toluidine toner | 4.75 parts |
1/2 sec nitrocellulose | 3.25 parts |
Dibutyl phthalate | 5.5 parts |
5 sec.ethyl cellulose (Ethoxy content less than 44 %) | 4.0 parts |
Paraplex rg2 | 8.75 parts |
Montan wax | 0.5 parts |
Shellac solution (6 lbs.cut) | 4.5 parts |
Butyl acetate | 12.25 parts |
Toluol | 43.5 parts |
Ethyl alcohol | 1.5 parts |
Petroleum naphtha | 2.5 parts |
Ethyl acetate | 9.0 parts |
The first three ingredients are dispersed in a banbury mixer and thereafter admixed with the rest. The finished composition has a viscosity of about 300 centipoises.
Paraplex rg2 is a resinous esterification product of straight chain dibasic acids such as adipic, sebacic etc and polyhydric alcohols such as glycerol, glycol and the like.
White ink for shellaced kymograph trackings:
Shellac varnish pigmented with titanium dioxide is very satisfactory as a white ink for use on shellacked kymograph paper.
Ink for printing on plastics:
A thermoplastic ink for printing on very thin aluminum or other non fibrous non-theroplastic bases (“carriers”) for later transfer on to plastics has the following composition.
Dewaxed bleached shellac | 75 parts |
Nitrocellulose | 25 parts |
The two are dissolved in alcohol to which a colouring matter id added.
This ink is used to produce a negative (of the final print required) on the carrier. When this is to be transferred to a thermoplastic moulding, it can be done any time when the article is moulded, as the negative will easily get transferred to the hot thermoplastic surface, leaving the non thermoplastic carrier. If the transfer has to be on to a thermosetting plastic, the moulding of the latter has to be interrupted before the article is fully cured. While the article is still hot, soft and tacky, the mould will have to be opened and the print free carrier removed from the moulded article. Alternatively, the carrier with the print may be placed in the proper place inside the mould itself and the moulding and transferring effected in one operation.
Transfer ink:
A solid transfer ink which can be printed in the fused state on paper which can be transferred, under mild or strong heat to other surfaces like leather, rubber, silk, cotton fabrics etc is prepared on the following composition.
Dewaxed bleached shellac | 5.00 parts |
Titanium dioxide | 1.000 parts |
Tricresyl phosphate | 0.50 parts |
Rosin | 5.00 parts |
Heavy grade lithographic varnish | 0.50 parts |
The shellac and titanium dioxide are mixed together and heated and kept in the molten state till the lac polymerises. The tricresylphosphate is then added and stirred, followed by the addition of the rosin and the varnish. The desired colouring matter such as bronze powders, dyes or pigments are then added and intimately mixed. The mett is then allowed to cool and solidify.
Printing of this ink on paper may be transferred to other surfaces with the help of a hot iron.
Printing compounds for transfer printing:
Printing compounds especially suitable for the printing, in high speed presses, of transfer patterns from which the printed design is to be transferred on to another surface like textile fabric etc. By moisture or by heat and moisture are prepared as follows:
Pure basic dye | 0.50 lb |
Acetin | 2.00 lb |
Dewaxed bleached shellac | 1.00 lb |
The shellac is stirred in the cold in the acetin and the mixture gradually heated to about 340ºF (171ºC). When the shellac has melted, the dye is added. For darker shades, the mixture is maintained at this temperature till all the dye has melted and got thoroughly mixed in. For light shades, the temperature may be reduced to 270ºF(132ºC) before the dye is added.
Methylene yellow, rhodamine, crystal violet, victoria blue, brilliant green and nigrosine are some of the dyes that can be used. Water thinned printing inks:
A non inflammable vehicle for printing inks suitable for use on rotogravure high speed presses is prepared from any of the following three compositions
I | II | III | |
Dewaxed bleached shellac | 10.00 | 10.50 | 15.00 |
Powdered borax | 5.00 | 6.25 | 7.50 |
Water | 85.00 | 81.25 | 77.50 |
The ingredients are heated together in a steam jacketed kettle or other suitable receptacle till a white foam appears on the surface. This is then allowed to cool and filtered. The composition should then mixed with emulsified oil prepared as below.
Cotton seed oil | 40 parts |
Powdered acacia | 10 parts |
Water | 50 parts |
The oil is triturated with the acacia. 4o parts of the water are then added and triturated followed by the addition of the remaining water. Pigments may then be incorporated.
Drawing, line and Indian inks:
Drawing, line and Indian inks are prepared from dewaxed bleached shellac aqueous solutions using borax. The pigments are milled in cold water and the dispersion mixed with the shellac solution.
Water proof drawing inks:
Water proof drawing inks are based on shellac solution in water containing ammonia and borax and synthetic dyes. Composition of the former and typical types suitable are given below:
Dewaxed bleached shellac | 50 gram |
Ammonia (0.90) | 90 ml |
Water | 360 ml |
Phenol | 1 gm |
Borax | 3 gm |
The lac is dissolved in the water containing the ammonia with gentle heating after which the remaining ingredients are incorporated. 50 ml of the cooled solution is then mixed with 50 ml of dye solution containing any of the following dyes in concentrations shown against each.
For colour | Dye | Qty in 50 ml of solution for 100 ml of the ink) |
Red | Erythrosine yellowish | 0.50 ml |
Orange | Brilliant orange r | 0.60 ml |
Yellow | Chloramine milling green b | 0.40 ml |
Green | Brilliant milling green b | 1.20 ml |
Blue | Wool blue g extra | 0.50 ml |
Violet | Methylk violet b | 0.50 ml |
Brown | Benzamine brown 3 go | 0.80 ml |
The following dyes may also be used but the water resistance of the ink will be somewhat inferior.
Red | Benzor fast orange s | 0.8 ml |
Red | Benzo fast orange s | 0.3 ml |
Brilliant groceine m | 0.3 ml | |
Orange | Orange r | 0.4 ml |
Yellow | Thiazol yellow | 0.8 ml |
Yellow | Metanil yellow | 0.8 ml |
Blue | New methylene blue n | 0.4 ml |
Violet | Crystal violet | 0.4 ml |
Brown | Benzo brown g | 0.6 ml |
Fluorescent Ink:
A fluorescent bright red colouring material (specifically an ink) is prepared of the following composition
Dewaxed bleached shellac solution | 250 parts |
Lithopone mixture | 200 parts |
Xylene red | 2 parts |
Quinoline yellow | 3 parts |
Water | 150 parts |
The shellac solution for the above is prepared by dissolving 100 parts of dewaxed bleached shellac in 250 parts of water and 50 parts of borax with the aid of heat. The lithopone mixture is made by grinding 50 parts lithopone and 1.5 parts of a dispersing agent ( a salt of a polymerised sulphonic acid resin) with 60 parts of water in a ball mill.
Marking Ink for Mica:
A water resistant mar proof marking ink for use on mica flakes has the following compositions
Dye (ammonia resistant)
Equal proportions of A and B are mixed together and then the dye incorporated.
Ink for making relievo-formes for printing:
An ink that will swell on heating and will trius be suitable for producing relievo formes for printing purposes is produced of the following composition.
Gum arabic (dry) | 9 parts |
Commercial water glass | 1 parts |
Autographic ink | 1 parts |
Shellac (5%) solution in spirit | 1 parts |
Venetian soap (dry) | 1 parts |
Colouring matter—water soluble-small quantity.
Solventless:
Embossing powders:
Dewaxed bleached shellac ground to suitable mesh, in conjunction with an appropriate pigment is used as an embossing powder.
Raised or thermographic printing:- special ink for.
The only resin which will not crack or peel off from raised printings is shellac. Special inks that improve the performance of shellac in this field and usable for raised printing on glass, metal and other non absorbent surfaces are made of the following compositions.
I
Paracoumarone resin | 100 parts |
Dibutyl phthalate | 100 parts |
Cobalt linoleate or acetate | 2.5 parts |
II
Boiled Linseed Oil | 73 parts |
Rosin | 8″ |
Carbon Black | 12″ |
Prussian Blue | 6″ |
III
Glycerine | 1.50 parts |
Dextrin | 1.00″ |
Anilin Colour | 0.25″ |
50% of the dibutyl phthalate may be replaced by an equal amount of butyl stearate. The shellac powder may be “set” in the printed ink in 100-150 c. When elastic characters in rounded relief will be obtained.
The amount of glycerin may be varied to suit the weather conditions.
Dull raised printing:
In raised printing or thermography, shellac gives glossed raised rounded prints. If a dull finish for the raised prints is desired, zinc stearate to the extent of 6 per cent on the weight of shellac may be incorporated. The shellac (100 parts) and zinc stearate (6 parts) may be ground separately to the appropriate mesh, mixed and gently warmed so that the stearate sticks to the shellac particles but the mixture does not fuse. Alternatively, the shellac may be fused with double the quantity, i.e. 12% of zinc stearate and the fused mass ground to the appropriate mesh.
Aluminium plamitate or megnesia may also be used to the same extent in place of zinc stearate for the same purpose.
Moisture or steam set printing inks:
Solutions of shellac in poly hydric alcohols from excellent vehicles for the formulation of moisture set printing inks. These inks are stable in press room humidity and are also fat and grease proof. The following are typical compositions.
A)Vehicle
Dewaxed Bleached Shellac | 40 parts |
Polypropylene Glycol (Boiling Range 230-300ºC) | 60 parts |
B) Inks
Colour | Vehicle (a above) by weight | Pigment | Parts by Weight |
Red | 76 | Lithol Red Toner | 24 |
Yellow | 40 | Chrome yellow | 60 |
Black | 80 | Carbon black | 20 |
Other water insoluble pigments or dyes may also be used in appropriate quantities.
Diethylene glycol | 50 parts |
“teglac” 127 and /or petrix acid | 40 parts |
Dewaxed Bleached Shellac | 10 parts |
Teglar 127 is rosin modified by an unsaturated poly-basic acid. Petrex acid is a terpene hydrocarbon of the formula c10h16 modified by an unsaturated polybasic acid.
Iii.press stable, moisture sensitive printing inks can also be made from vehicles obtained by dissolving shellac in a liquid polyhydric alcohol and adding to the solution certain nitrogen containing compounds such as amides, imides, amines, ammonia or ammonium salts. These inks are stable to small amounts of water but insoluble in an unlimited amount of water. typical compositions are indicated in table 1.
The shellac, polyhydric alcohol and nitrogenous compound are heated together at the temperature indicated in column v a till a homogeneous melt is obtained. Column v b indicates the approximate time taken to reach this stage. Where this is left blank, this stage is reached by the time the temperature indicated is reached. In the case of ammonia (composition 13), the gas is passed through a warm solution of the shellac in the glycol. The product is then allowed to cool and forms the vehicle.
For preparing the inks, these vehicles are milled with the pigments indicated in column vi c and vi d together with the additional solvents wherever necessary as indicated in column vi a and vi b. Needless to say that the pigments are interchangeable. Appropriate quantities of other desired pigments may also be used.
Prints from these inks can be heat set or steam set. The inks may also be used for printing on moist paper which may then be set by heat.
Printing inks with high humidity tolerance, capable of being set by steam and useful for typographic printing with fast or slow operating presses can also be prepared by esterifying shellac with dicarboxylic acids or their anhydrides, in the presence or absence of mutual solvents, and dissolving/di dissolving/dispersing the product in a polyhydroxy alihatic alcohol. In table 2 shown typical compositions.
The shellac and the acid or anhydride are finely powdered and intimately mixed together, with or without the mutual solvent (column iii), and heated to the temperature indicated in column v a and maintained for the period indicated in column v b. The polyhydric alcohol indicated in column vi is then gradually added and the product maintained at the temperature indicated in column vii till dissolved. When a volatile solvent is used, the heating has to be conducted under a reflux condenser.