Pharmaceutical Industry
Uses of Bleached Shellac in Pharmaceutical Industry.
Uses of Bleached Shellac in Pharmaceutical Industry
Dewaxed Bleached Shellac dissolved in specifically denatured alcohol are the glazes employed for coating pharmaceutical tablets and confectionery by the pan method.
The main uses for Dewaxed Bleached Shellac in the pharmaceutical industry are for coating tablets and sustained release capsules.
The functions of the shellac, depending on the particular medicament are:
- To serve as a moisture barrier, protecting the core ingredients
- As an enteric coating
- To control disintegration
- As a granulating agent
- As a finishing coat over wax, prior to the printing of a trademark.
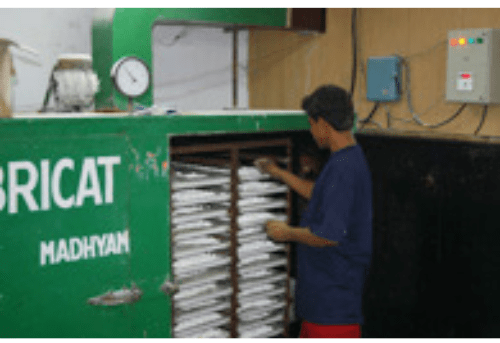
The shellac is normally applied by the pan method from alcohol solutions, the concentration of shellac depending on the function to be performed. In practice the number of coats applied depends on the function of the shellac coating and varies from as few as 1 or 2 coats for a moisture barrier, to as many as 16 or 20 coats for enteric coating.
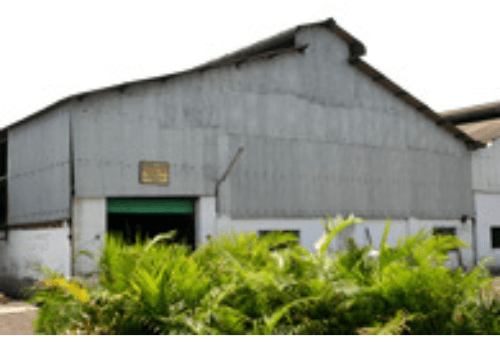
Our Dewaxed Bleached Shellac give almost colourless transparent films of great clarity and brilliance with increased water-resistance and higher stability. Films from these do not polymerize and lose their solubility in weak alkalis so rapidly as those from bleached lac and maintain a more stable disintegration time upon ageing.
Procedure: Charge the coating pan, clean and dust-free, with tablets so that they tumble freely.
Start the coating pan at 38-48 r.p.m. and add just enough shellac glaze to cover the tablets. Mix the tablets by hand to ensure even distribution of the glaze.
Allow the tablets to roll until they begin sticking to the pan and to each other. At this point, add a small amount of dusting agent, such as talc, and again mix by hand.
When the tablets are rolling freely, blow in air at room temperature for 5 to 10 until most of the remaining alcohol is driven off and then dry with warm air at 29-39ºC for 25 to 40 minutes. The tablets are then cooled and the procedure repeated as many times as needed. Allow 48 hours of air drying before starting to re-coat.